Spent hours this afternoon doing the rings which are going well with a few niggles but found a real problem (of course).
Positives of the Day:
Gapped the rings using Peter's grinder which works a treat. This grinder is a luxury compared to needle files. You made me smile Peter!

One piston at a time matched to the barrel. Done 4 , 2 to go. All gaps were too tight, so managed to tweak then bang on.
Top ring has to be 17 thou, second ring 6 though wider, so 23 thou.
Generally the top ring as supplied was 12 to 15 thou and the second 18 max.
The real sod is getting the oil control ring set in, what a game but my skill is getting better with practice and no swearing. Patience is not my middle name but you just have to take your time.
Negative of the Day:
The C clips to retain the wrist pins are HUGE compared to the Porsche items. So thick and REALLY difficult to get into the piston grove.
My home made (from soft duralumin) was ovalized by the resistance to fit the clip. I did get one in place but silly effort.
Asked the piston supplier if the clips were correct and they are. He wished me luck.
There is no way you an fit these clips when assembling the engine using fingers and a screwdriver. I know I can fit 6 beforehand but they are murder with the piston in a vice!
Going to remake my Stompski knock-off tool in steel and see if that works. I doubt the Stompski tool would grapple with these clips.
The bad weather continues here, so should get Saturday to finish the cylinders and a bit more. Doubt my steel will arrive.
Will also contact the rolling road man to see how he feels about th Clewett ignition system, the simple (cheap) one.
It should at least bolt on and work, right?
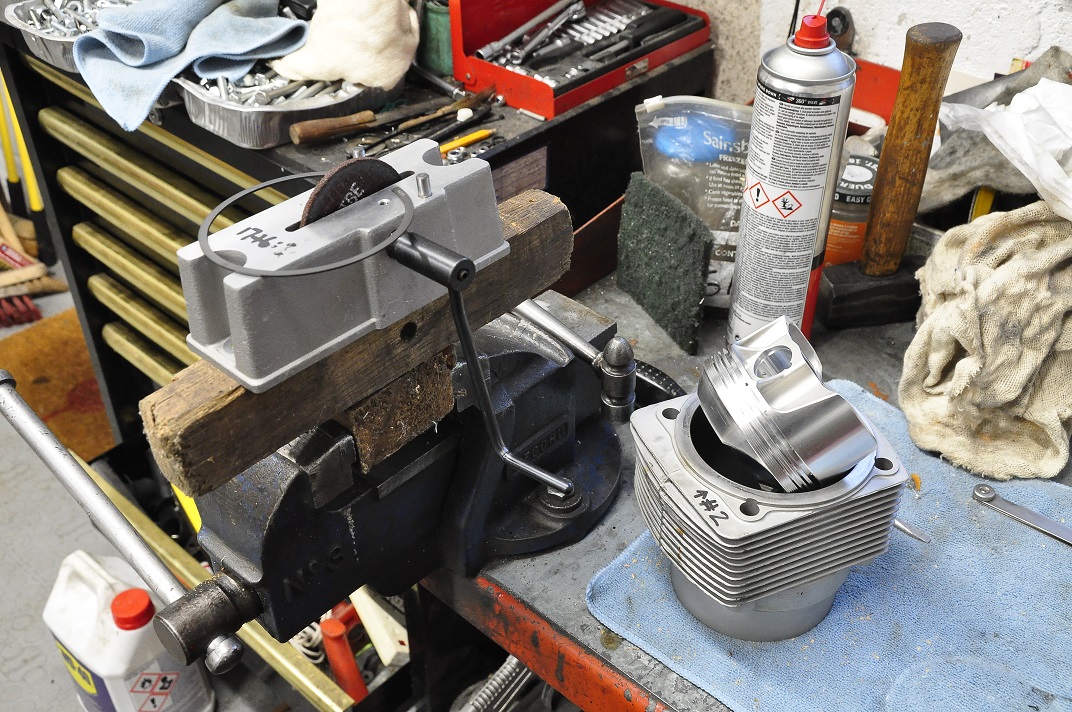
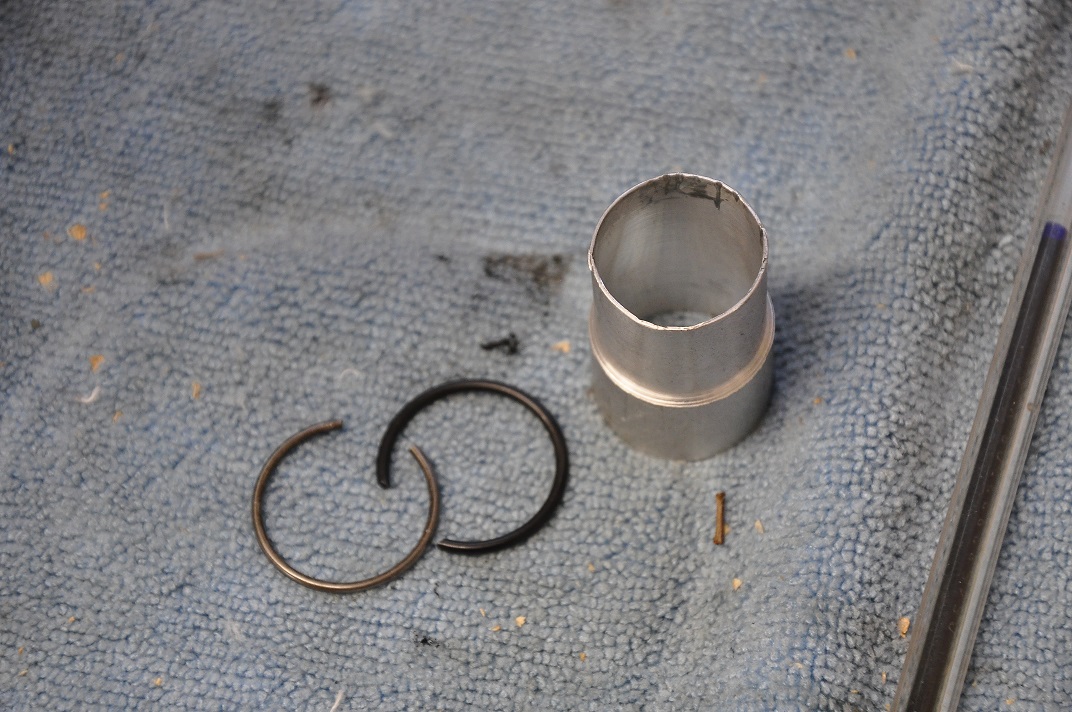